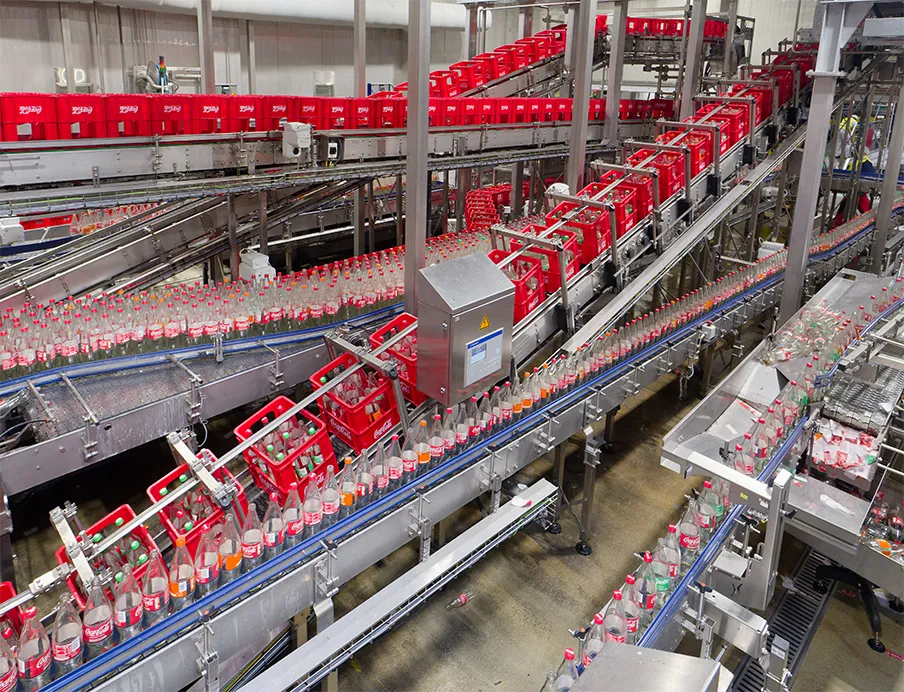
Coca-Cola betreibt als weltweit größter Getränkehersteller allein in Westeuropa über 50 Abfüllstandorte. Um Wartung und Störungen schnell und präzise anzugehen, digitalisiert der Konzern alle Abfüllanlagen und entwickelt dafür einen digitalen Zwilling. Damit können Produktionsprozesse in Echtzeit überwacht und bei Bedarf sofort optimiert werden, sogar remote von jedem Ort weltweit. Für die erforderliche zuverlässige Sensorik arbeitet Coca-Cola eng mit dem Automatisierungsspezialisten Ifm zusammen. Einer der Vorzeige-Standorte liegt in Edelstal in Österreich.
„Wir sind ein lizenzierter Abfüllbetrieb für Coca-Cola und füllen hier fast alle Produkte ab", erklärt Christian Kohlhofer, Plant Manager, Coca-Cola HBC Österreich. Mit über 500 Millionen Liter abgefüllten Getränken pro Jahr zählt das Werk zu den größten der Gruppe. „Wir fokussieren uns hier stark auf die Themen Automatisierung und Digitalisierung. Vieles, was wir umsetzen, wird anschließend auch in anderen Werken des Konzerns umgesetzt“, so Christian Kohlhofer. Das Werk in Edelstal agiert auch als Kontingentwerk: Wenn an anderen Standorten Produktionsengpässe auftreten, kann das österreichische Werk einspringen und andere Standorte unterstützen.
Condition Monitoring vermeidet ungeplante Stillstände
Die Anlagenverfügbarkeit hat oberste Priorität für den internationalen Getränkehersteller. „Bei uns hier am Standort merken wir jeden einzelnen Anlagenstillstand deutlich“, erklärt der Plant Manager. Schließlich produziert man just in time und kann nicht auf Vorrat arbeiten. Deshalb setzt man auf Predictive Maintenance mit Condition Monitoring. Das heißt, der Zustand von Maschinen und Anlagen wird permanent überwacht, um Wartungen genau dann durchzuführen, wenn sie nötig sind. Echtzeitdaten von Sensoren werden genutzt, um Verschleiß, Abnutzung und anderen Instandhaltungsbedarf frühzeitig zu erkennen. Ziel ist es, ungeplante Stillstände zu vermeiden, Wartungskosten zu senken und die Lebensdauer der Anlagen zu verlängern. Mit Einsatz von IO-Link, IoT und maschinellem Lernen können Wartungsarbeiten so geplant werden, dass sie genau im richtigen Moment stattfinden. Das heißt, es wird nicht zu früh und nicht zu spät gewartet.
„Durch die zahlreichen Sensoren, die verbaut worden sind, erhöhen wir deutlich die Anlagenverfügbarkeit", freut sich Kohlhofer. „Wir machen die Wartung nicht mehr zeitbasiert, sondern zustandsabhängig. Das reduziert signifikant unsere Kosten."
IO-Link-Sensoren überwachen bei Coca-Cola komplexe Prozesse
Wenn es um die Digitalisierung von Anlagen geht, sind Sensoren mit IO-Link-Schnittstelle die erste Wahl. Diese intelligenten Sensoren nutzen eine standardisierte, bidirektionale Kommunikationsschnittstelle, um mit Steuerungen und anderen Systemen zu kommunizieren. Im Gegensatz zu herkömmlichen Sensoren ermöglichen sie nicht nur den Austausch von einfachen Schaltsignalen, sondern auch von umfangreichen Prozessdaten und Diagnoseinformationen. Da die Übertragung der Messwerte digital und nicht analog erfolgt, ist diese zudem störsicher und exakt. Denn im Gegensatz zur analogen Übertragung treten keine Wandlungsverluste auf.
Die Sensoren lassen sich einfach installieren und konfigurieren, bieten präzise Daten in Echtzeit. Über azyklisch abrufbare Diagnosedaten, etwa Minimal- oder Maximalwerte, Verschmutzungsgrad oder Fehler wie Drahtbrüche oder Kurzschlüsse, wird die zustandsorientierte Wartung unterstützt. Zudem sorgen IO-Link-Sensoren für hohe Flexibilität und Effizienz in der Automatisierung. Durch ihre hohe Kompatibilität können sie nahtlos in bestehende Systeme integriert und aufgrund der digitalen Kommunikation einfach in die IT-Ebene eingebunden werden.
Dosenverschließprozess: IO-Link-Sensoren registrieren kleinste Vibrationsabweichungen
Ein Beispiel bietet der Einsatz von IO-Link-Schwingungssensoren am Dosenverschließprozess. „Über die Qualität im Prozess der Dosenverschließung entscheiden Tausendstelmillimeter“, erklärt Gerhard Wieszmüllner, Maintenance & Spare Parts Manager bei Coca-Cola HBC Österreich. „Mit den prädiktiven IO-Link-Sensoren von Ifm können wir kleinste Vibrationsabweichungen feststellen und somit eine garantiert vollständig und dauerhaft verschlossene Dose gewährleisten."
An den Klappenventilen der Flaschenwaschanlage sind IO-Link-Ventilsensoren von Ifm im Einsatz. „Wir bemerken im Vorfeld, wenn eine Klappendichtung kaputt geh bzw. ausgetauscht gehört, ohne jeglichen Materialverlust", so Gerhard Wieszmüllner. „Dadurch brauchen wir zum Beispiel keine Laugenbäder ablassen und haben keine Maschinenstillstände von großer Dauer. Das spart uns Zeit und Kosten.“
Über den Y-Weg zum digitalen Zwilling
Um den Zustand der Maschinen und ihrer Komponenten genau zu beurteilen, werden sämtliche Sensordaten der Anlage erfasst. Dabei kommt der sogenannte Y-Weg zum Einsatz, bei dem die Sensordaten in Echtzeit auf zwei Pfade aufgeteilt werden: Einerseits gelangen die Daten in die SPS, die die klassische Steuerung und Regelung der Anlage übernimmt. Gleichzeitig fließen die digitalen Sensordaten über einen zweiten Pfad in die IT-Ebene. Bei Coca-Cola werden die Signale der zahlreichen Sensoren auf diese Weise automatisch in die IT-Plattform "Pocket Factory" übertragen. Dieses virtuelle Abbild spiegelt als digitaler Zwilling die reale Anlage exakt wider und wird kontinuierlich mit Echtzeitdaten aktualisiert.
KI und Machine Learning prognostizieren rechtzeitig Verschleiß und Produktionsfehler
Durch die Digitalisierung bis auf Sensorebene erhält Coca-Cola volle Transparenz über seine weltweite Produktion. Der digitale Zwilling, gestützt auf Daten der IO-Link-Sensoren von Ifm, ermöglicht die zustandsbasierte Wartung der Anlagen. Mithilfe von Machine Learning und künstlicher Intelligenz werden Verschleiß, Produktionsfehler und andere Anomalien im Prozess frühzeitig prognostiziert. „Diese Daten erlauben uns, proaktiv und zum optimalen Zeitpunkt die richtigen Instandhaltungsmaßnahmen durchzuführen, um die Produktqualität zu sichern", erklärt Wieszmüllner. So lassen sich ungeplante Stillstände vermeiden, Kosten senken und die hohen Qualitätsansprüche gewährleisten.
Digitale Technologien unterstützen Coca-Cola bei der Nachhaltigkeit
Ein weiterer wichtiger Aspekt der Digitalisierung bei Coca-Cola ist die Nachhaltigkeit. Durch den Einsatz digitaler Technologien kann der Konzern seinen ökologischen Fußabdruck reduzieren. Beispielsweise ermöglicht die präzise Überwachung und Steuerung der Produktionsprozesse eine effizientere Nutzung von Ressourcen wie Wasser und Energie. Das ist nicht nur gut für die Umwelt, sondern hilft auch, Kosten zu sparen.
Cybersecurity-Anforderungen erfüllt
Cybersecurity spielt in einem Produktionswerk wie dem von Coca-Cola eine zentrale Rolle. Hier geht es nicht nur darum, sensible Unternehmensdaten, sondern auch kritische Produktionsprozesse vor unbefugtem Zugriff und Manipulation zu schützen. Durch die zunehmende Vernetzung von Maschinen und Anlagen in der Industrie 4.0 steigt das Risiko für Cyber-Angriffe auf die Infrastruktur. Ein erfolgreicher Angriff könnte nicht nur zu Produktionsausfällen, sondern auch zu erheblichen finanziellen Schäden oder Image-Verlust führen. Zudem sind in einem Werk oft Systeme im Einsatz, die produktionskritische Daten verarbeiten, beispielsweise zur Qualitätssicherung oder Effizienzsteigerung. Der Schutz dieser Daten gewährleistet, dass Betriebsgeheimnisse gewahrt bleiben und die Prozesse sicher und stabil ablaufen. In einem stark regulierten Umfeld, wie es bei Coca-Cola der Fall ist, müssen alle Komponenten, einschließlich der eingesetzten Sensoren, strengen Cybersecurity-Anforderungen entsprechen, um den sicheren Betrieb der Anlage und die Integrität der Produktion zu gewährleisten.
„Ifm hat es geschafft, gemeinsam mit unserem internen Cybersecurity-Team Wege zu finden, um alle Standards einzuhalten", lobt der Plant Manager Christian Kohlhofer. „Die Daten werden so abgelegt, verarbeitet und ausgewertet, dass alle Cybersecurity-Richtlinien erfüllt werden."
Coca-Cola pflegt enge Partnerschaft mit Ifm
Seit vielen Jahren arbeitet Coca-Cola am Standort in Österreich eng mit Ifm als Automatisierungspartner zusammen. Plant Manager Christian Kohlhofer lobt die Partnerschaft: „Ifm hat ja den Slogan ,Close to you'. Das passt zu unserem internen Wert ,We over I'. Wir arbeiten beide gemeinsam an einer guten Zusammenarbeit und sind an schnellen Lösungen interessiert", so der Manager. „Ifm ist immer da, wenn man sie braucht und gerade bei Problemen extrem schnell in der Reaktionszeit."
Fazit: Coca-Cola steigert Effizienz durch Digitalisierung und Automatisierung
Die Digitalisierung und Automatisierung bei Coca-Cola ist ein fortlaufender Prozess, der den Konzern in die Zukunft führt. Durch den Einsatz modernster Technologien und die enge Zusammenarbeit mit Partnern wie Ifm kann Coca-Cola seine Produktionsprozesse optimieren, die Effizienz steigern und die Qualität seiner Produkte sicherstellen. Gleichzeitig trägt die Digitalisierung dazu bei, die Nachhaltigkeit zu verbessern und die Umweltbelastung zu reduzieren. Mit einem klaren Fokus auf Innovation und kontinuierliche Verbesserung ist Partnerschaftliche Zusammenarbeit von Coca-Cola und Ifm bestens gerüstet, um auch in Zukunft erfolgreich zu sein.